Air Permitting Challenges for RNG Processing Facilities
June 10th, 2022By: Tom Rolfson, P.E., Air Quality Engineer, POWER Engineers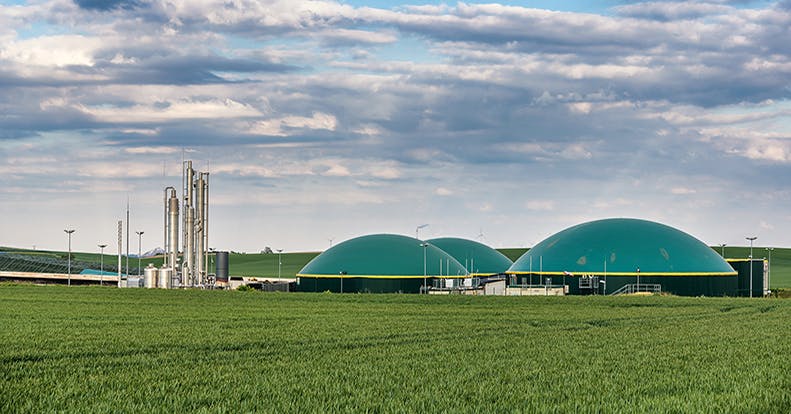
Due to increased societal pressure to address climate change, the production and use of renewable natural gas (RNG) has seen significant growth in the last few years. According to the Environmental Protection Agency (EPA), operational RNG projects have more than tripled since 2017. While landfills have typically made up the majority of operational RNG projects, the bulk of new growth has come from agricultural digester projects.
The idea behind RNG is simple: take methane that would otherwise be released into the atmosphere as a greenhouse gas (GHG) and convert it into a product compatible with existing natural gas infrastructure.
Putting this concept into practice, however, is quite complex. Although RNG has decarbonization (carbon-reducing) benefits, there are a number of technical engineering and air permitting challenges that must be addressed in the plant design to ensure a project maintains compliance with environmental regulations.
Background: RNG and CO2e
Biogas contains roughly 45-65% methane, 35-55% carbon dioxide (CO2) and trace amounts of other gases. There are thousands of sources across the country where biogas is captured, primarily from landfills, wastewater treatment plants and dairy or swine farms.
Many operators of these methane sources currently process biogas to generate RNG—particularly landfills, as previously stated. Others, however, either combust (flare) or vent the raw biogas, because there have not been enough incentives historically to justify the increased cost of producing RNG.
When CO2 equivalent (CO2e) emission reductions are quantified, it becomes evident why the RNG industry is growing so rapidly. Methane has a greenhouse effect 25 times higher than that of CO2 and from a biogas source it can be:
- Released to the atmosphere as fugitive emissions.
- Combusted in a flare.
- Processed into RNG and injected into a natural gas pipeline for eventual use.
When methane is released into the atmosphere as a fugitive emission, it represents the worst-case GHG emission scenario. While there are some associated fugitive and direct CO2e emissions involved with processing both RNG and geologic natural gas, they offset each other to an extent. RNG has the ability to reduce certain biogas carbon emissions by approximately 90%.
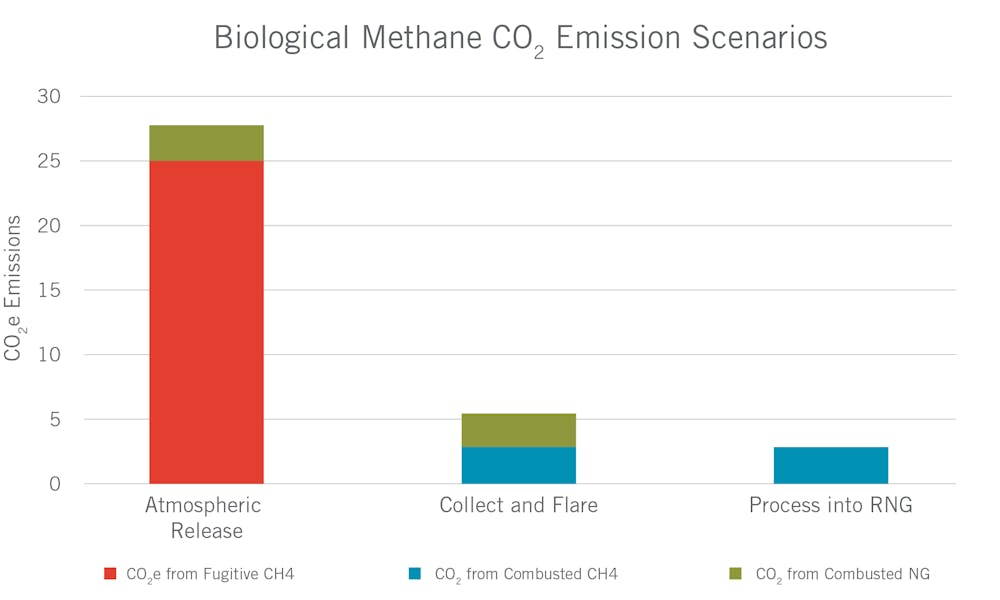
The three fates of biological methane (CH4) include fugitive atmospheric release, collection and flaring, or processing into useful RNG. When released to the atmosphere or collected and flared, CO2 is also emitted from the combustion of natural gas (in green) that the RNG would otherwise replace.
Plant Design Air Permitting Considerations
The typical air permitting considerations for an RNG processing plant are similar to those of other process emission sources. The unique challenges for RNG processing plants relate to quantifying hydrogen sulfide (H2S) and sulfur dioxide (SO2) emissions, accommodating changes to feedstock waste, and conducting H2S and SO2 dispersion modeling. These nuances create additional complexities and become interconnected with plant design.
Quantifying H2S vs SO2 Emissions
Any developing project involving air pollutant emissions must secure either an air permit or exemption prior to construction. However, as with many developing projects, the design may not be finalized before a permit is required.
In some instances—and particularly for RNG processing plants—the project design relies on aspects of air permitting, especially the quantification of emissions. Because quantifying emissions can be a trial-and-error process, there are often multiple iterations of emission calculations and design modifications. Permit classifications are generally based on the facility-wide potential emissions, and the potential emission levels for an RNG processing facility can vary widely.
Because H2S is destroyed when combusted and the sulfur converts to SO2, it is important to understand the emission quantification consequences of where the H2S removal system exists in the process flow. For example, if the H2S removal is upstream from the flares, the resulting SO2 emissions will likely be relatively low and therefore have minimal effect on the permit classification.
If the H2S removal is downstream from the flares, on the other hand, the potential emissions may be quite high. In some cases, it could be well over 200 tons per year, so a permit classification may result in more burdensome permit conditions. In other cases, state or local regulating authorities may have specific rules that drive the project design and factor heavily into the permit classification.
Consider a scenario where a state regulation affects the design of an RNG processing plant. If the state regulation limits SO2 emissions from process sources to 10 pounds per hour (lb/hr), when emission rates are higher than this limit, emission controls (or a Best Available Control Technology analysis, demonstrating why those controls are not justified) are required.
In this scenario, a project developer makes initial plans for the H2S removal to be downstream from the facility flare, so that during plant outages or downtime, the biogas would be flared. However, the biogas composition is relatively high in H2S content with an emission rate of approximately 50 lb/hr SO2.
If the initial plant design was made before preliminary air permitting activities and before the state regulation was identified, a revision to the design would require the H2S removal to be upstream from the flare. The result: different gas processing and H2S removal techniques due to the site-specific nature of the biogas source.
The new design would qualify for a more streamlined air permitting process since, with H2S removal coming before the flare, the SO2 emission rate from the upstream flare would be less than 1 lb/hr.
Accommodating Changing Waste Trends
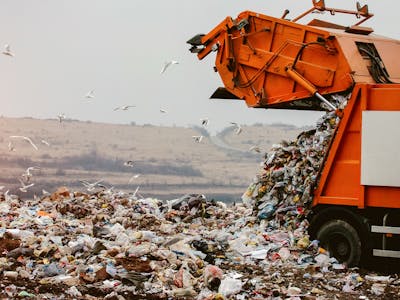
While the design of the RNG processing plant is one challenge, the characteristics of the waste itself is another. Dairy and swine biogas are relatively consistent long-term, as is wastewater biogas. Landfill gas, however, is dependent on the composition of the waste entering the landfill. Changing waste trends can have a significant impact on the quality and quantity of raw landfill gas that RNG producers capture and process.
In the past 60 years, waste recycling, yard waste composting and other waste management trend changes have led to decreases in organic waste at landfills. As a result, many landfills are seeking non-traditional sources to replace some of the municipal solid waste (MSW) contracts. Depending on regional trends, these landfills are accepting industrial and commercial construction and demolition debris and industrial process wastes, such as sludges and oil and gas drilling fluids.
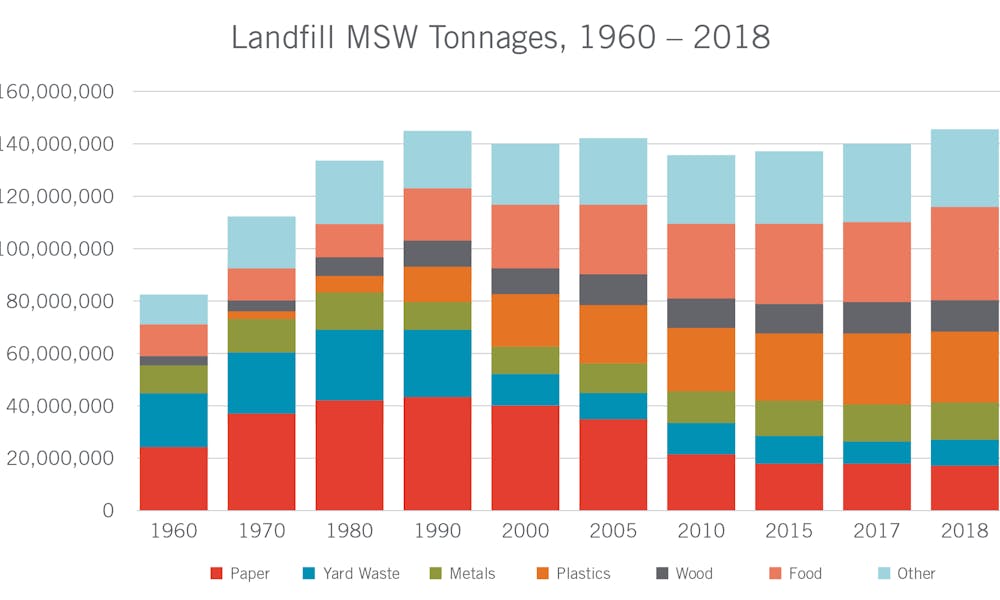
Changing waste trends and waste disposal techniques have shifted the amounts of certain materials landfilled since 1960. Note the significant reductions in paper and yard waste landfilling since their peak in the 1980-1990 timeframe. The “other” category includes glass, rubber, leather, textiles and other miscellaneous wastes. These seven categories represent the types of landfilled MSW wastes.
These changing waste trends can have an adverse impact on air permitting compliance. Let’s consider a facility that developed an RNG processing plant at a landfill in 2007. Using historical waste trends to establish gas characteristics, the facility was initially permitted to flare raw landfill gas with H2S contents up to 400 parts per million (ppm).
Years later, however, an influx of gypsum board from construction and demolition debris changed the waste trends at the landfill. Gypsum, otherwise known as calcium sulfate dihydrate, is known to increase the concentration of H2S in landfill gas. Consequently, H2S contents in the raw landfill gas begin to reach levels as high as 1,000 ppm and averaged well over 400 ppm.
Consequently, emission rates from the facility flare begin to exceed the permit limits, resulting in challenges with air permitting compliance. While the state agency understands the problem, they require a permit amendment application to re-establish appropriate permit limits. The application also requires air pollutant dispersion modeling to address the since-promulgated one-hour SO2 National Ambient Air Quality Standard (NAAQS), which is a health-based limit on the atmospheric concentration of SO2 with a limitation of 75 parts per billion in ambient air.
Dispersion Modeling of H2S and SO2
Air pollution dispersion modeling analyses at RNG processing facilities typically focus on compliance demonstrations for state-level H2S ambient standards and the one-hour SO2 NAAQS. As explained previously, any H2S present in a combusted gas will result in SO2 emissions. If the gas is vented, the hazardous nature of H2S will likely require modeling to meet the stringent ambient air quality standards.
Venting arrangements do not provide ideal dispersion characteristics. Lower temperatures, flowrates and stack heights can be problematic for demonstrating compliance with applicable H2S air quality standards. What happens if a high H2S content gas is combusted? The one-hour SO2 NAAQS can be a challenge to meet when conducting dispersion modeling.
The one-hour SO2 NAAQS has a complex statistical definition that led EPA to provide specific guidance on how to approach compliance demonstrations, which is colloquially known in dispersion modeling circles as the “intermittent source guidance.”
To simplify this complex and confusing technical issue, the EPA guidance states that, because of the statistical nature of the one-hour NAAQS, emission scenarios that are infrequent and unpredictable are not necessary to include in such modeling analyses. Although the EPA guidance has specifically focused on exemptions for intermittent NOx emissions (i.e., emergency generators or combustion turbine startups and shutdowns), this guidance can be extrapolated for use in intermittently-used flares that are combusting high H2S content biogas.
In the previous example, the elevated H2S content of the raw gas being flared requires an air permit amendment application with air pollutant dispersion modeling. The facility needs to demonstrate compliance with the one-hour SO2 NAAQS, which did not exist in 2007, when the plant was initially permitted. The concern about elevated SO2 emission rates is made more difficult because of the stringent NAAQS. The intermittent source guidance includes documentation about historical raw gas flaring events. These are submitted to support the determination, solving the problem of elevated H2S.
Complex Projects, Complex Permitting
RNG processing facilities face technical engineering challenges that can be solved in various ways. RNG processing equipment, H2S removal systems, feedstock gas characteristics and state and local regulations may vary at each project site.
These technical challenges apply to everything from plant design to air permitting and compliance. Though many RNG processing facilities may be relatively small in comparison to other oil and gas fuel processing facilities, the air permitting considerations remain significant.
Ensuring compliance for the lifespan of a facility must be addressed through good planning and expert analysis during the air permit application process, before the plant design is finalized.
author
Tom Rolfson
Air Quality Project Manager
Tom has extensive experience in air quality permitting and compliance, air emission inventories, air dispersion modeling, and multi-media environmental compliance. His project experience includes Clean Air Act New Source Review and Title V Air Permitting projects, as well as environmental compliance oversight for industrial, manufacturing and institutional clients. Tom also assists clients with strategic planning for capital projects and proposed state and federal air regulations, and has experience representing clients in communications with local, state and federal regulating authorities. He has also prepared and certified numerous oil SPCC plans, conducted multi-media environmental compliance audits and prepared EPA hazardous chemical reports.
Related Content
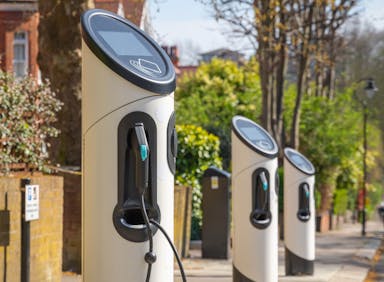
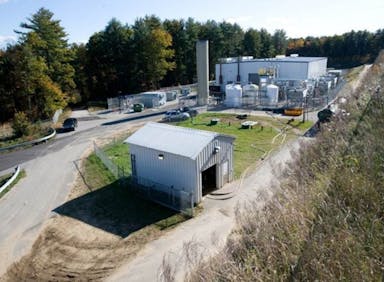